“The Black Face of the Deep Sea”
Development of the Seiko Professional Diver’s 600m Watch
Since the time of its launch in June 1975, Seiko’s Professional Diver's 600m watch has been held in high esteem by many professional divers. Even today, over 40 years later, it continues to evolve and improve, while at the same time carrying on the original concept of the first-generation Professional Diver's 600m watch. Here, we present the history of its development.
※This article is largely a reproduction of an article submitted to the Kokusai Tokei Tsushin international clock and watch industry magazine (No. 442; published in January 2009) by Taro Tanaka, who was development leader and designer of the Professional Diver's 600m watch.
-
STORY 01
Where It All Began: A Single Letter of Complaint
-
The impetus for the initial development of the Professional Diver's 600m watch was a single letter of complaint, received by K.Hattori & Co. (now Seiko Watche Corporation) in 1968. The letter read as follows:
“I am a diver who works at depths of 350m using a diving bell. When diving to such depths, we can pressurize to 35 atmospheres (ATM) over a short period of time before diving. However, after diving, we must use a decompression chamber to depressurize gradually. The ocean floor is an extremely harsh environment in which to work, and Seiko’s current 300m specification diver’s watch is unfit for use...”
-
STORY 02
Is the Current Diver’s Watch Unfit for Use?
-
The 300m Diver’s watch, which was unfit for use in saturation diving Unfit For Use?
The Seiko professional diver’s watch of the time was a 300m waterproof specification design developed in 1968. In order to achieve maximum waterproof performance, the watch employed a one-piece construction unlike any other; even those not seen in Swiss-made designs. Seiko adopted a specially hardened inorganic glass for the glass portion of the watch that would completely block the entry of moisture, so the developers were confident in its water-resistance capabilities, and found it hard to believe the words written in the letter: that the watch was unfit for use.
”Let’s hear what this diver has to say!”
The Seiko developers decided that they should listen in more detail to what the diver who wrote the letter had to say. After requesting to do so, the diver amicably visited K.Hattori & Co. His name was Yo Oshima; a professional diver working for a company called Nihon Kaiyo Sangyo (which later became Sumitomo Marine Development).
-
STORY 03
What is Saturation Diving?
-
What Mr. Oshima told the developers included a string of diving-related information and terms that the developers had never even heard before; from diving work on petroleum drillships and saturation diving using helium to diving bells and decompression chambers. At any rate, the one thing that the developers were able to clearly ascertain was that, apparently, their 300m specification diver’s watch was unfit for use. When the developers asked Mr. Oshima to show them the drillships and diving equipment, and to tell them in more detail about saturation diving, he happily agreed.
-
STORY 04
Visiting a Petroleum Drillship
-
Looking up at a petroleum drillship (or “rig”), viewed from a distance The drillship was anchored at Kure Port in Hiroshima Prefecture. Seiko sent two members of staff to visit: myself Taro Tanaka, development leader at Seiko, and Mr. Akabane, an engineer from the design section of Suwa factory.
What we saw at Kure was literally beyond our wildest imaginings. We boarded a motor boat and headed offshore, but even when the guide pointed and said “That’s it!” we could not see anything that seemed like the kind of ship that we were looking for. But looking harder, we saw a massive turret-like structure with several cranes mounted on top of it, towering above the water surface. This, we were told, was the drillship or “rig.” The kind of vessel one might typically imagine upon hearing the word ship was nowhere to be seen.
-
STORY 05
Diving Bells & Decompression Chambers
-
(Left) A spherical underwater elevator (diving bell) is lowered into the water using a cable (Right) A saturation diving mask which delivers a gas mixture of helium and oxygen Diving Bells
“This is a diving capsule, or ’bell,’” we were told. What we saw was a kind of spherical, underwater elevator. A team of two divers boards the diving bell, which is pressurized in advance to the same pressure as the seabed where the divers will work, using a helium-oxygen gas mixture. After the pressurized bell is lowered to the required depth, the divers swim out to begin their work. The inside of the bell was an extremely narrow, confined space, and it was not even possible for us to take pictures.
The photograph on the left shows a spherical diving bell (underwater elevator) being lowered into the water using a cable. Gas cylinders filled with helium-oxygen gas mixture are fitted to the bottom part of the spherical bell.An onboard deck-mounted decompression chamber, showing the entrance/exit hatch Decompression Chambers
We were also shown the decompression chamber where, we were told, the divers spend several days after completing their dive in order to decompress gradually. The decompression chamber is a large, cylindrical capsule installed onboard the ship. However the inside of it is a confined space in which it would not be possible to stand and walk around.
-
STORY 06
The Compelling Comments of the Professional Divers (Needs & Requests with Regard to Diver’s Watches)
-
The comments (problem points) that remained strongly with us upon hearing Mr. Oshima and his fellow divers speak in detail about the realities of saturation diving and the role of a diver’s watch, were as follows. Eventually, these comments would become the impetus for the creation of the Professional Diver's 600m watch watch.
Concerning the Movement
1. Divers have to carry out underwater electrical welding, so the watch’s resistance to magnetism is a concern.
2. The question of whether or not the watch will stop during a dive is a concern.
3. Divers also wear their watches while on land, in order to verify their reliability.
Concerning the Hands & Dial
1. Divers check the passage of time every few minutes during a dive.
2. It is difficult to see the time when the light/visibility is dim. Divers need to be able to tell the time easily even in complete darkness.
Concerning the Watch Case
1. Cables often become entwined around divers’ wrists and the watch itself while in the confined space of the diving bell, or while working on the ocean floor; which is a bothersome nuisance for divers.
2. When two divers are crammed into the confined space of the diving bell, it is dangerous if there are any sharp or pointed parts on the watch.
3. Since divers accidentally bang their wristwatches into various places, they soon become covered in scratches and damage.
4. The watch frequently malfunctions while the divers are in the decompression chamber after completing their dive.
5. If the watch is dropped the deck of the ship, the crown (winding knob) will typically come off, or the glass will crack, and the watch will break.
6. When carrying out maintenance on diving equipment onboard the ship, grease/oil gets into the gap between the rotating bezel and the body of the watch. It is difficult to remove this grease/oil even when the watch is cleaned with petroleum, which presents a problem for divers.
7. Shirts and suits quickly become damaged from rubbing against the rotating bezel.
Concerning the Watchstrap
1. At the low temperatures experienced on the ocean floor, the existing (PVC plastic) watchstrap hardens, and becomes brittle and easily breakable (i.e. snaps easily).
2. Even when the watch strap is fastened tightly before diving, it becomes loose when working on the ocean floor due to the water pressure.
Concerning the External Appearance of the Watch
1. Divers would like the watch to be stylish enough for them to wear it out on formal occasions when they are overseas, etc., without feeling embarrassed.
While I did feel that it would be difficult (or impossible) to resolve all of these compelling concerns, after seeing the professional divers risking their lives working in deep sea environments, I resolved firmly—as the development leader, and as an industrial designer—to take on board all of the comments made by the divers; and to attempt to resolve these problems.
-
STORY 07
Solutions to Problems with the Movement
-
Concerning the Movement
1. Divers have to carry out underwater electrical welding, so the watch’s resistance to magnetism is a concern.
2. The question of whether or not the watch will stop during a dive is a concern.
3. Divers also wear their watches while on land, in order to verify their reliability.
The distinguishing characteristics that are demanded in a watch movement that can withstand the rigors of saturation diving are resistance to shock, vibrations and magnetism, and a high level of torque to drive and support the hands of the watch, which must be made larger (and therefore heavier) in order to improve visibility.
・We adopted the same Cal.6159 movement as in the 300m Diver’s watch. The 61 series was the most reliable movement available at the time, with the best actual track record, and was also installed in the Grand Seiko series of watches.
・We inserted an anti-magnetic sheet between the bottom of the watchcase and the movement itself, dramatically increasing its resistance to magnetism.
-
STORY 08
Solutions to Problems with the Hands & Dial (In Pursuit of Improved Visibility)
-
Concerning the Hands & Dial
1. Divers check the passage of time every few minutes during a dive.
2. It is difficult to see the time when the light/visibility is dim. Divers need to be able to tell the time easily even in complete darkness.
The face of the dial was given a black satin finish. The hour markings were printed in white, with a white luminous paint coating; and the hour, minute and second hands were given a special rainbow finish to emphasize their metallic texture.
・The hour markings, excluding the 12 o’clock marker, were created as circular markings that would appear to shine most brightly and efficiently with the luminous paint even in darkness; while the 12 o’clock marker was created as a triangular marking in order to make it readily distinguishable from the other markers at a single glance.
・The minute hand was made extremely wide and fat, to make it immediately visible over all other features of the watch. Various other devices were also employed to make the minute hand readily distinguishable from the hour hand, including differences in the placement of the luminous paint, and in the size and shape of the hands themselves.
・A large-sized circle of luminous paint was applied to the second hand to enable divers to verify that the watch is working properly in dimly lit environments, or even in pitch darkness.
・The world’s first white luminous paint—NW luminous*—was adopted for use on the watch. Even when viewed during daylight, the markings appear clear and easily visible, and the use of this coating enabled Seiko to design the watch with a precise and luxury-feeling dial, and hour, minute and second hands for the watch.
*Seiko requested for the specialist chemical manufacturer Nemoto & Co., Ltd. to develop a luminous coating for luxury items.
-
STORY 09
Solutions to Problems with the Case
-
Concerning the Watch Case
1. Cables often become entwined around divers’ wrists and the watch itself while in the confined space of the diving bell, or while working on the ocean floor; which is a bothersome nuisance for divers.
2. When two divers are crammed into the confined space of the diving bell, it is dangerous if there are any sharp or pointed parts on the watch.
3. Since divers accidentally bang their wristwatches into various places, they soon become covered in scratches and damage.
4. The watch frequently malfunctions while the divers are in the decompression chamber after completing their dive.
5. If the watch is dropped the deck of the ship, the crown (winding knob) will typically come off, or the glass will crack, and the watch will break.
6. When carrying out maintenance on diving equipment onboard the ship, grease/oil gets into the gap between the rotating bezel and the body of the watch. It is difficult to remove this grease/oil even when the watch is cleaned with petroleum, which presents a problem for divers.
7. Shirts and suits quickly become damaged from rubbing against the rotating bezel.
There were a wide-range of problems to be solved in relation to the watchcase, all of which presented difficulties.
・We devised a case structure whereby the rotating bezel was mounted onto a one-piece inner body, and covering it with a just-fitting outer body (i.e. a dismantle-able case construction). We thought that, by doing so, we could enable to easily disassemble the case and remove the outer body (holding down the rotating bezel) from the inner body, simply by removing the four fixing screws; enabling each part to be individually washed and cleaned, even when caked in grease/oil. Additionally, in order to increase corrosion resistance and make the watch more lightweight, we decided to adopt a titanium case; which was a first for a diver’s watch.
・We gave the outer body a conical shape, and rounded both the upper and lower edges to eliminate the danger of having sharp edges. By having the outer body function as a guard, we were able to prevent ropes and cables from becoming entangled around the rotating bezel and crown (winding knob), and protect the watch from the impact of droppages. It also enabled us to remove the risk of damage to shirts, sweaters, suits and other items of clothing during everyday use.
・Aside from the bare minimum of exposed space cut out along the edge of rotating bezel (between the 2 o’clock and 8 o’clock positions) to allow wearers to rotate the bezel with their fingers, we covered the bezel with the outer body in order to remove the risk of the bezel shifting out of place or being rotated unintentionally.
・In order to ensure that the watch’s crown (winding knob) does not obstruct the movement of the wearer’s wrist during diving work, damage the wearer’s dry suit, or suffer direct impact shocks even when dropped on the ship’s deck, we chose to position it at the 4 o’clock position; the same position as on the 300m Diver’s watch.
・By adopting flat glass, we were able to lower the surface of the glass face of the watch to below the level of the upper surface of the rotating bezel; thereby significantly reducing the risk of the glass surface breaking or becoming otherwise scratched or damaged.
・In order to prevent scratches and other damage to the outer body of the case, we developed a technology in which a super-hard coating material is sprayed onto the outer body at high temperature; a technology commonly referred to as our “black thermal spraying” treatment.
Aside from the problem points described above, there were also many other difficult problems to be resolved in terms of design, technical and manufacturing aspects. The main problems in these areas were as follows.
・In order to prevent the intrusion of helium (which has small-sized molecules) into the internal parts of the watch, we had to fundamentally rethink the packing materials and fixing methods used to seal the edges around the watch’s glass face and crown (winding knob).
・We had to ensure that the watch could withstand the stresses of not only pressurization but also decompression.
・We had to enhance the watch’s water and corrosion resistance over long periods of time.
・We adopted titanium (strong, lightweight and corrosion resistant) for use in the fabrication of watchcase.
・We also had to ensure that the inside surface of the glass would not cloud up due to differences in temperature.
In order to overcome these difficulties, we began conducting research into these technical aspects immediately after the inspection visit to Kure Port.
-
STORY 10
Solutions to Problems with the Watchstrap
-
Concerning the Watchstrap
1. At the low temperatures experienced on the ocean floor, the existing (PVC plastic) watchstrap hardens, and becomes brittle and easily breakable (i.e. snaps easily).
2. Even when the watch strap is fastened tightly before diving, it becomes loose when working on the ocean floor due to the water pressure.The accordion-style polyurethane watchstrap ・We adopted polyurethane for the material of the strap, in place of the PVC plastic used in the original watch (which becomes hard, brittle, and easily breakable at low temperatures). Polyurethane does not harden easily at low temperatures. At the time, polyurethane was finally starting to be used in other industries, and Seiko was the first in the watch industry to adopt the material for a watch strap.
・Taking a hint from my passion for photography, I also came up with the idea of making part of the strap similar in shape to the accordion-style expandable section sometimes seen on folding cameras; enabling the creation of an expandable/contractible watchstrap.
-
STORY 11
In Order to Fulfill Requests Concerning External Appearance
-
Concerning the External Appearance of the Watch
1. Divers would like the watch to be stylish enough for them to wear it out on formal occasions when they are overseas, etc., without feeling embarrassed.
・We made numerous prototypes and worked to refine the various elements of the design: including the shape, texture and color of the outer case (the part that is most eye catching), the rotating bezel, crown (winding knob) and strap; the mutual balance of these elements and the overall operability of the watch when all of these elements are combined as one; the feel and comfort of wearing the watch; its sense of presence, and the atmosphere or aura that it exudes.
-
STORY 12
Design Efforts: (Problems & Solutions for the Hands, Dial, Case & Watchstrap)
-
A conceptual sketch summarizing the design created to resolve the various problems with the watchcase. The idea that we arrived at in order to resolve the various problems with the case, after trying numerous different contrivances, was a case construction in which we mounted the rotating bezel onto a one-piece inner body and covered it with a just-fitting outer body.
The illustration on the left is a conceptual sketch, created in order to gain the understanding of the staff in the relevant departments at Suwa Seikosha with regard to the overall design of the watch; which was necessary because the shape and design is completely different from that of a normal wristwatch.One part of the initial prototype drawings sent to Suwa Seikosha The illustration on the right is a drawing illustrating the ideas that we devised for the structure and shape of the watchcase, in order to resolve the various case-related problems; which was created during the very initial stages of the development as one part of the prototype drawings sent to Suwa Seikosha for technical consideration. At this stage, the screw ring that holds down the rotating bezel was still attached separately on top of the outer body of the watch. It was later incorporated into a single, one-piece construction.
-
STORY 13
Listening to the Opinions of Professional Divers...
-
Once the prototype for the new watch was complete, we asked Mr. Oshima and his fellow divers to try using it in an actual diving environment to check whether there were any faults or defects, asked their opinions about whether there were any points that we should improve upon further, and made various alterations and adjustments to the design. We also showed the prototype to various other people, and listened to their opinions. We also frequently visited Mr. Akira Tateishi of the Marine Art Center Co., Ltd. (a leading underwater photographer and publisher of the monthly magazine Marine Diving) to hear his opinions on the watch.
-
STORY 14
Twenty New Patents, Utility Model and Design Registrations
-
Twenty new patent, utility model and design registrations were made in relation to the Professional Diver's 600m watch, including those for the newly proposed dismantle-able case construction and design, the high-visibility dial and hand designs, and the expandable/contractible watchstrap shape design.
-
STORY 15
“This thing isn’t a wristwatch!”
-
The reaction when we first presented our new watch design to other members of the company was, “What’s this big black thing? This isn’t a wristwatch!” However, after we explained that the project had begun with a letter of complaint, and that this was the design that we had arrived at as the result of a technical process in pursuit of solutions to resolve the various problems, there were no more negative reactions. The final verdict was that since it was a specialist timepiece we should at least launch it onto the market in the hopes of arousing topical attention.
-
STORY 16
Finally, On to the Sales Launch!
-
The Professional Diver's 600m watch made its commercial debut in June 1975, at a retail price ¥89,000. After its initial launch, the watch soon gained widespread recognition amongst professional divers for its high-level functionality, performance, reliability and durability, which were unparalleled by other manufacturers both in Japan and overseas; eventually earning the watch its reputation as “the world’s greatest diver’s watch.”
-
STORY 17
Shifting from Mechanical to Quartz, and the Addition of a Day-Date Function: The Professional Diver's 600m watch Becomes a Super-Long-Seller Product
-
In 1978, the watch made the transition from a mechanical movement to quartz, with the adoption of the Cal.7549 movement. The cuffs of the outer body that had surrounded the bezel in the 12 o’clock and 6 o’clock directions were cut down to reduce the overall weight of the watch, and the hour, minute and second hands were improved further for even greater visibility. The inner body, rotating bezel, crown (winding knob) and external fixing screws on the outer body were given a near-golden coloring to add a touch of shine and glamor to the watch’s external appearance. The retail price rose to ¥120,000.
In March 1986, when the movement was changed to a Cal.7C46 movement, the material used in the outer body was changed to a high-strength black ceramic, and the watch‘s resistance to water pressure was enhanced to withstand diving to depths of up to 1,000m. The retail price rose to ¥133,000.
Even today, over 40 years later, the Professional Diver's 600m watch continues to maintain its reputation as the world’s greatest diver’s watch, with no changes to its basic concept or image.The quartz version of the Professional Diver's 600m watch In 1978, the watch made the transition from a mechanical movement to quartz, with the adoption of the Cal.7549 movement. The cuffs of the outer body that had surrounded the bezel in the 12 o’clock and 6 o’clock directions were cut down to reduce the overall weight of the watch, and the hour, minute and second hands were improved further for even greater visibility. The inner body, rotating bezel, crown (winding knob) and external fixing screws on the outer body were given a near-golden coloring to add a touch of shine and glamor to the watch’s external appearance. The retail price rose to ¥120,000.
In March 1986, when the movement was changed to a Cal.7C46 movement, the material used in the outer body was changed to a high-strength black ceramic, and the watch‘s resistance to water pressure was enhanced to withstand diving to depths of up to 1,000m. The retail price rose to ¥133,000.
Even today, over 40 years later, the Professional Diver's 600m watch continues to maintain its reputation as the world’s greatest diver’s watch, with no changes to its basic concept or image.
-
STORY 18
“Whatever happens, surely at least this watch will continue working as if nothing had happened!”
-
Seiko has received virtually zero complaints concerning the durability or water resistance of the watch since its launch. The comment that “surely the watch will continue working” is a comment that we often hear from people who have used the Professional Diver's 600m watch. As a developer, these are the ultimate words of praise.
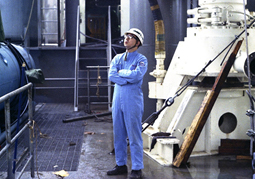
The design of the first-generation Professional Diver's 600m watch was an inevitable process of the pursuit of a revolutionary design, emerging from the unfiltered voices of Seiko’s customers.

There are clear reasons behind each and every part of the design, which was created in the pursuit for reliability, functionality, usability and high visibility in a diver’s watch. In 2017, at the Baselworld watch and jewelry fair, the very latest Professional 1000 (which is descended from the original, first-generation Professional Diver's 600m watch) was applauded as having the most beautiful face of any diver’s watch.
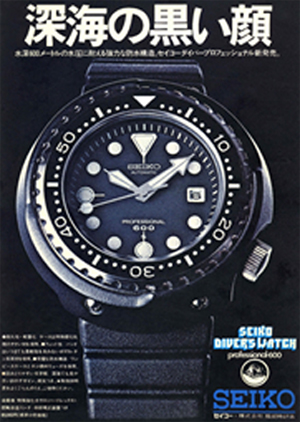
The first-generation Professional Diver’s 600m watch gained a reputation as the world’s greatest diver’s watch, and established Seiko’s image for high quality timepieces. The method of its development (a style of manufacturing in which creators come together as one with the users, with the aim of creating the very best products) also subsequently became the standard Seiko style of product development for future projects, and also became the impetus for the creation of numerous other sports watches.