Improvements of parts
Throughout the history of the escapement’s evolution, clockmakers and watchmakers sought to minimize errors due to friction by striving to reduce the period of interference from the wheel as much as possible through the entire oscillation cycle of the pendulum or balance wheel.
Even today, watchmakers continue to make developments in line with this course of evolution, such as increasing precision by reducing the friction and weight of the escapement, improving driving efficiency, and extending the time between overhauls by eliminating the need for oiling of the escapement.
An increasing number of manufacturers are using silicon materials not only for the hairspring, but also for the escape wheel and pallet fork. This is because silicon has a smooth surface and is both hard and light, which means that it can reduce accuracy errors caused by friction while also reducing the frequency of oiling. If the regulator and escapement become magnetized, not only can this throw out its accuracy, it can even stop the escapement’s motion altogether. But one of the qualities of silicon materials is that they cannot be magnetized. Yet another benefit to silicon is that even parts with complicated shapes can be mass produced with high manufacturing precision.
Although silicon is hard, it is brittle under impact, and for this reason Seiko does not use it.
Instead, Seiko manufactures its escape wheels and pallet forks from nickel alloys using MEMS (Micro Electrical Mechanical Systems), a high-precision component-manufacturing technology adapted from the semiconductors industry. Because the surfaces of metallic parts manufactured by MEMS are extremely smooth, there is little friction, and because of the high manufacturing precision, the driving efficiency is increased.
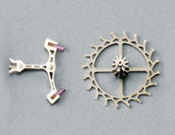
Moreover, because it is possible to manufacture hollow components, weight can be reduced. By implementing an oil-retaining structure on the tips of the escape wheel teeth, Seiko has helped to reduce the number of times the mechanism needs to be oiled.
A new breed of mechanical watches
In order to completely eliminate errors due to friction between the pallet fork and the escape wheel, Seiko also developed an ingenious mechanism called the Spring Drive to replace the regulator and escapement. Although it is a mechanical watch that uses the force of an unwinding spring to drive the gear train, it does not use a balance, a pallet, or an escape wheel. Instead, the IC applies a magnetic brake on the rotation of the last wheel of the gear train (the rotor), based on a signal provided by a quartz oscillator, to precisely control the rotational speed at 8 Hz. Through this mechanism, the Spring Drive achieves the same level of precision as a quartz watch.
High precision mechanical watches
Seiko is one of the few watch manufacturers still producing 10-beat high-precision mechanical watches. The background factors to this are Seiko’s high technology-development capabilities that have allowed it to develop both the mainspring (the engine of the watch) and the hairspring (the heart of the watch), starting from the materials used, and the craftsmanship of skilled technicians to adjust the hairspring.
From the late 1960s to the 1970s, the only thing expected of the 10-beat watches of those times was high precision, but today’s consumers want watches that are also long-lasting, durable, and anti-magnetic. In order to meet those needs, a manufacturer must be able to develop a new mainspring that can provide strong energy, a hairspring that can harness that limited power efficiently and economically, and an escape wheel and a pallet fork that are both lightweight and durable. Through this kind of comprehensive technological capability, Seiko is able to produce high-precision 10-beat watches with optimal energy balance and driving efficiency.